Auf Einladung von thyssenkrupp haben wir in der Nähe von Aachen an einem Driving Event teilgenommen und uns angeschaut, welche Rolle der Konzern, den man in der breiten Öffentlichkeit eher mit der Stahlproduktion assoziiert, mittlerweile in den technologieintensiven Bereichen der Automobilindustrie spielt. High-Tech statt Hochofen.
Tribond Stahl: leichter, fester – und weicher
Selbstverständlich wurde auch über Stahl gesprochen. Der Werkstoff und die in den vergangenen Jahrzehnten gewandelten Produktionsverfahren sind ein elementarer Bestandteil im Fahrzeug- und Karosseriebau, mit weitreichenden Auswirkungen. Neue Fertigungsverfahren und die Kombination verschiedener Werkstoffeigenschaften können z.B. enorme Konsequenzen für das Gewicht eines Fahrzeugs haben, womit sich sowohl bei Elektrofahrzeugen als auch bei Fahrzeugen mit Verbrennungsmotoren Einsparungspotentiale in puncto Strom und Kraftstoff ergeben. Nach eigenen Angaben ist thyssenkrupp der einzige Automobilzulieferer, der maßgeschneiderte Werkstoffverbunde für die Autoindustrie anbieten kann.
Den “Stahl der Träume” für einen Automobilhersteller müsst ihr euch ungefähr so vorstellen: Er soll bei maximaler Festigkeit und hoher Duktilität (Verformbarkeit) so leicht wie nur irgendwie möglich sein.
Insbesondere bei crashrelevanten Strukturteilen wünscht man sich zum einen Festigkeit, um die strukturelle Integrität zu gewährleisten – aber auch Verformbarkeit, um Aufprallenergie bei einem Unfall aufzunehmen und die Insassen zu schützen. Das alles klingt nach einem Widerspruch, einem Dilemma: Wie soll etwas gleichzeitig möglichst fest und trotzdem möglichst gut verformbar sein?
Die Lösung liegt im “Sandwich”, bei dem thyssenkrupp zwei verschiedene Stahlsorten miteinander kombiniert. Die – stellt es euch einfach so vor – Brotscheiben sind „weiche Stähle“ die eine hohe Verformbarkeit besitzen. Der “Belag” in der Mitte des “Sandwichs” besteht hingegen aus einem hochfesten Stahl mit sehr geringer Verformbarkeit. Dieses Sandwich mit einer Gesamtdicke von 3 Zentimetern wird dann mit einem speziellen Verfahren auf eine Dicke von z.B. 5 Millimeter gewalzt. Das Ergebnis ist ein Blech, aus dem sich Bauteile fertigen lassen, die sowohl höchste Festigkeit als auch hohe Energieaufnahmen durch Faltenbildung kombinieren.
Ein willkommener Effekt zusätzlich zum Plus an Sicherheit für die Fahrzeuginsassen ist eine mögliche Gewichtsersparnis von bis zu 10% (!), was sich positiv auf den Verbrauch und damit auf die CO2-Bilanz von Fahrzeugen auswirkt.
Auch Elektroautos benötigen weiterhin Stahl, zudem spielt der Werkstoff eine enorme Rolle bei der Stromversorgung. Sowohl beim Bau von Elektromotoren als auch bei der Übertragung von Energie kommt den Materialeigenschaften der Komponenten eine besondere Rolle zu. In beiden Bereichen ist es wichtig, dass der Strom mit möglichst geringen Verlusten transportiert und genutzt wird. thyssenkrupp bietet hier mit dem Elektroband einen Stahl an, mit dem besonders wenig Magnetisierungsverluste auftreten.
[parallax-image caption=““]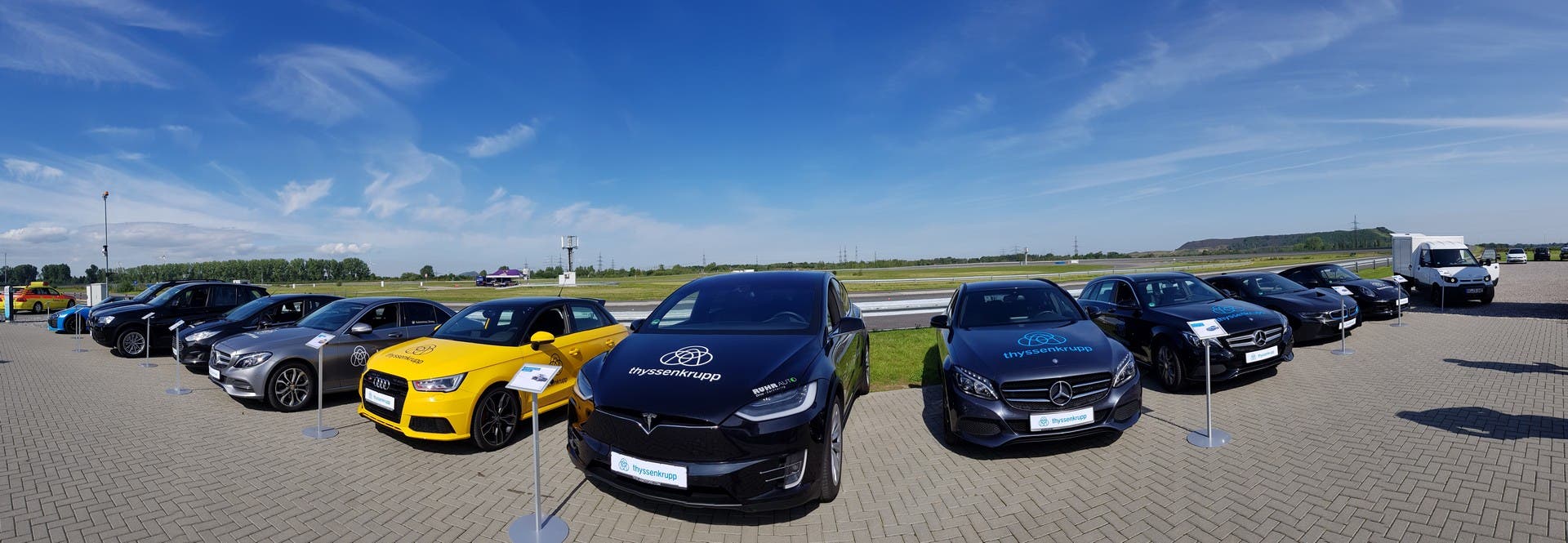
Wie aus Kohle eine Felge wird
Ein auch für uns überraschendes Geschäftsfeld von thyssenkrupp als Zulieferer der Automobilindustrie war das Engagement im Bereich Karbon. Das Unternehmen unterstützt ein Team in der Formula Student. In dieser Klasse entwickeln Teams von mehreren Hochschulen einen eigenen Rennwagen und treten dann gegeneinander an. In Zusammenhang mit diesem Engagement ist die Idee für Felgen entstanden, die vollständig aus Carbon bestehen.
Carbon wird vielen von euch aus dem Sportwagenbau bekannt sein, hier wird das Material sehr oft verwendet. Man schätzt den Werkstoff wegen seiner hohen Festigkeit und seinem geringen Gewicht. Die Verarbeitung von Carbon ist allerdings überaus aufwändig. Ein Rad, das vollständig aus Carbon in großer Serie produziert werden kann, hat die Ingenieure vor einige Herausforderungen gestellt.
Der sogenannte Felgenstern wird noch relativ traditionell im sogenannten Schichtverfahren ausgeformt und gehärtet. An den Rändern des Sterns bleibt Material überlappend übrig. Mit diesem überlappenden Material wird dann der Rest des Rades an den Stern verwoben! Die Maschine, die für diesen Webvorgang benötigt wird, hat einen Durchmesser von 9 (in Worten: neun) Metern. Insgesamt werden für die Fertigung des Rades 15 Kilometer Carbonfaser verwebt – das ist wirklich beeindruckend und wir werden in den nächsten Wochen einmal versuchen, euch eine solche Maschine zu zeigen.
Am Ende des Verarbeitungsprozesses steht eine Felge, die nicht nur knapp 30 Prozent leichter sein soll, sondern auch noch um einiges stabiler als eine traditionelle Leichtmetallfelge ist. Auch hier ergeben sich Einsparungspotentiale, Komfort- und Sicherheitsaspekte: So übertragt das Rad durch die eigene hohe Festigkeit weniger Schwingungen auf das Auto bzw. Fahrwerk und die Karosserie.
Bei dem Rad aus Carbon handelt es sich also um ein komplettes Hightech Produkt, das momentan vor allem für Premiumhersteller von Sportwagen und deren Kunden besonders interessant sein dürfte. Von der Idee über die Entwicklung der Maschine bis hin zur Serienreifen hat es fünf Jahre gedauert. Diese Zeitspanne macht deutlich, welche Entwicklungszyklen in der Automobilindustrie gelten, bis alle relevanten Parameter (Material, Verarbeitung, Sicherheit, Preis, Serienreife) optimal aufeinander abgestimmt sind. Das Resultat der Geduld: thyssenkrupp ist jetzt der einzige Hersteller, der seinen Kunden eine solche Maschine anbieten kann. Neben der Ingenieursleistung finde ich auch besonders interessant, wie sich das Unternehmen neben seinen klassischen Geschäftsfeldern aufstellt und dabei auch in Technologien und Produkte investiert, die nahezu gar nichts mehr mit der ursprünglichen Herstellung von Stahlerzeugnissen zu tun hat.
Vom Fahrwerk zum autonomen Fahren
Während des eigentlichen Driving Events konnten wir jede menge zum Thema Fahrwerksdämpfer lernen. Die thyssenkrupp-Tochter Bilstein ist eines der weltweit führenden Unternehmen im Bereich der Herstellung von Dämpfungssystemen für die Automobilindustrie. Angefangen hat alles mit den sogenannten passiven Dämpfersystemen. Diese Systeme wurden so eingerichtet, dass sie ein möglichst breites Spektrum abdecken und in möglichst vielen Fahrzeugen eingesetzt werden konnten. Es gibt allerdings keine Möglichkeiten, diese passiven Systeme einzustellen.
Heute ist es jedoch so, dass die meisten Dämpfersysteme verschiedene Fahrweisen wie „Normal“, „Sport“ oder „Komfort“ unterstützen. In heutigen sogenannten adaptiven Systemen erfassen Weg- und Beschleunigungssensoren kontinuierlich jede Fahrzeugbewegung und stellen die Dämpferhärte automatisch für jedes einzelne Rad je nach Untergrund und Fahrverhalten individuell ein. Dabei werden im Stoßdämpfer ein oder mehrere Ventile elektronisch angesteuert, die je nach Signal den Ölfluss innerhalb des Systems regeln. Dadurch wird der Durchflusswiderstand für das Öl beim Ein- und Ausfedern des Dämpfers verändert und somit die Dämpfkräfte stufenlos und in Bruchteilen von Sekunden angepasst. Da mit einer solchen Regelung nur die Energie der Radbewegungen genutzt wird, um gezielt Kräfte zu erzeugen, die die Karosseriebewegungen verringern, spricht man auch von semiaktiven Systemen.
Intelligente Fahrwerke mit “Noise Cancelation”
Durch autonome Fahrzeuge wird den Dämpfern in mehr oder weniger naher Zukunft eine noch größere Bedeutung zukommen. Denn wenn das Auto irgendwann einmal vollkommen selbstständig fährt, können wir als Passagiere unsere Zeit ganz anders nutzen. Untersuchungen haben aber gezeigt, dass heutzutage fast 40% aller Menschen an der sogenannten “Reisekrankheit” leiden, wenn sie sich einer Fahrt länger auf etwas anderes konzentrieren als auf das Fahren bzw. Die vor ihnen liegende Strecke.
Um in Zukunft noch mehr Komfort für die Autoinsassen zu gewährleisten, entwickelt thyssenkrupp bereits ein neues aktives Dämpfunggsystem. Die Fahrbahn wird gescannt und man stellt gezielt eine Gegenkraft ein, mit der die zu erwartende Schwingung der Bodenunebenheit ausgeglichen werden soll. Das dahinterstehende Prinzip lässt sich gut mit einem Noise Canncelation System vergleichen, das man ja aus dem bereich der Kopfhörer kennt.
Auf der Teststrecke in Aldenhoven bei Aachen hatten wir die Möglichkeit, mit verschiedenen Dämpfersystemen zu fahren und so die Unterschiede zu spüren. Der Fahrcharackter der verschiedenen Fahrzeuge war teilweise dramatisch verändert, einen guten Eindruck von den Probefahrten erhaltet ihr in unserem Video.
Lenkrad 3.0: Autos steuern – wie im Airbus
Obwohl unsere Autos immer moderner geworden sind, haben sich viele Bauteile nicht wirklich verändert. Sie sind über die Jahre “nur” moderner und effizienter geworden. Als Beispiel seien naheliegenderweise der Verbrennungsmotor und das Getriebe genannt. Auch heute, fast 100 Jahre nach der ursprünglichen Erfindung des Autos, haben die meisten Wagen noch einen Verbrennungsmotor und ein Getriebe mit Handschaltung.
Ähnlich verhält es sich auch mit dem Lenkrad. Das Grundprinzip des Lenkens hat sich nicht großartig verändert. Eine Stange führt vom Lenkrad in den Motorraum und ist dort mechanisch mit dem Lenkgetriebe verbunden. Viele Autos besitzen zwar heute schon elektrisch unterstützte Lenksysteme. Ein Elektromotor unterstützt die Lenkbewegung bei Bedarf und sind damit eine wesentliche Voraussetzung zur Erhöhung der Fahrsicherheit. Assistenzfunktionen, wie Einparkhilfe, Spurwechsel- bzw. Spurhalteassistent und Abstandswarner wären ohne elektrische Lenkunterstützung nicht möglich.
Doch der nächste technologische Entwicklungsschritt ist ein Steer-by-Wire System. Ähnlich wie in Flugzeugen des Herstellers Airbus gibt es in Fahrzeugen mit diesem Lenksystem keine durchgängige mechanische Verbringung zwischen Lenkrad und Rädern – vor ein paar Jahren wäre so etwas noch undenkbar gewesen.
Im Prinzip lässt sich das System sehr gut mit einem Force-Feedback-Lenkrad, das man von Computerspielen kennt, vergleichen. Sensoren messen die Lenkimpulse des Fahrers und geben sie per Kabel an ein Steuergerät weiter. Dieses gibt dann die passenden Befehle an den Elektromotor weiter, der die Räder entsprechend einstellt. Selbstverständlich will man beim Fahren aber auch eine entsprechende Rückmeldung im Lenkrad spüren. Dies wird über den sogenannten Feedback-Aktuator realisiert.
Wie im Flugzeug werden die Steer-by-Wire Systeme über entsprechenden Redundanzen verfügen, sofern eine Einzelkomponente ausfallen sollte. Speziell für autonome Fahrzeuge wird das Steer-by-Wire System wichtig sein, denn wenn das Auto selbst fährt sind Hersteller in der Lage das Lenkrad einfahren zu lassen, so dass die Insassen mehr Platz haben. Auch die passive Sicherheit wird durch die Technologie erhöht, den im Falle eines Crashes fehlt die Lenkwelle, die enorme Kräfte in den Fahrgastraum transportieren könnte. Das Fehlen der Lenkwelle bedeutet zudem, dass der Motorraum keine Verbindung in den Fahrgastraum hat und die Autos damit noch ruhiger im Innenraum werden können.
Wir hatten die seltene Möglichkeit, einen von thyssenkrupp mit einem Steer-by-Wire System ausgestatten Sportwagen der Marke Roning probezufahren, seht euch das Video einfach mal an. Beim Fahren konnte ich keinen Unterschied zu einem Fahrzeug mit klassischer Lenkung feststellen. Das Lenkgefühl war absolut realistisch. Bei einem rein elektronischen System lässt sich dann natürlich auch das Lenkverhalten des Wagens ganz gezielt auf die gewünschten Parameter einstellen. Bei dem schon sportlichen Testwagen konnte man die Lenkung spürbar sportlicher einstellen. In meinem jugendlichen Leichtsinn 😉 habe ich natürlich einen Ausflug in die Auslaufflächen neben der Teststrecke gemacht. So bleibt mir das Event nicht nur wegen meines kleinen Abstecher ins Grüne lange in Erinnerung, sondern auch wegen dem Einblick in die verschiedenen Technologien.